ビーズミルとインライン測定器を組み合わせた運転システム
はじめに
粉砕・分散工程において、粒子径や粘度、ゼータ電位などを制御することは品質管理や製品特性向上、コストダウンの面からも非常に重要です。多くの製造現場では経験や計算値から粉砕・分散工程の管理を行っていますが、この様な管理方法では機器構成部材などの磨耗や原料品質のばらつきなどによって、製品が品質規定範囲から外れてしまうロットが出てくる可能性があります。ここでは、ビーズミルの処理中にリアルタイムで粒度分布とゼータ電位の測定ができる測定システムを紹介します。
インライン測定器の原理
当社で使用しているインライン測定器は、電気音響法と超音波減衰法の2種類の測定方式を組み合わせて、粒度分布とゼータ電位を測定するシステムです。
超音波減衰法では粒度分布測定が可能です。粒子が分散したスラリに超音波を照射すると、超音波はスラリ中を通過する際に減衰します。超音波の減衰は粘性損失、熱的損失、散乱損失などが主に関係しますが、粒子濃度と粒子径に大きく依存します。したがって、既知の粒子濃度で測定すれば、計測された減衰率から粒子径を算出することができます。
電気音響法では、粒度分布測定とゼータ電位の測定が可能です。帯電した粒子が分散したスラリに交流電圧を印加すると、粒子は振動して交流電場と同じ周波数の超音波を発します。大きな粒子は小さな粒子と比べて慣性モーメントが大きいため低速でしか動けず、交流電場の振動速度に追随しきれず、遅れを生じます。この位相のずれの大きさから粒子径を算出することができます。また、大きなゼータ電位を持った粒子は、小さなゼータ電位の粒子と比べて早く振動し、強い音波を発することができるため、測定された超音波の強弱からゼータ電位を算出できます。
上記で紹介した2つの測定原理にはそれぞれ得手不得手があります。例えば、超音波減衰法は電荷を帯びていない粒子の測定が行うことができますが、電気音響法では原理的に難しいとされています。この様に2つの測定原理を併用することで、互いのデメリットをメリットによって補い合い、より幅広いサンプル条件で測定が行なうことが可能です。
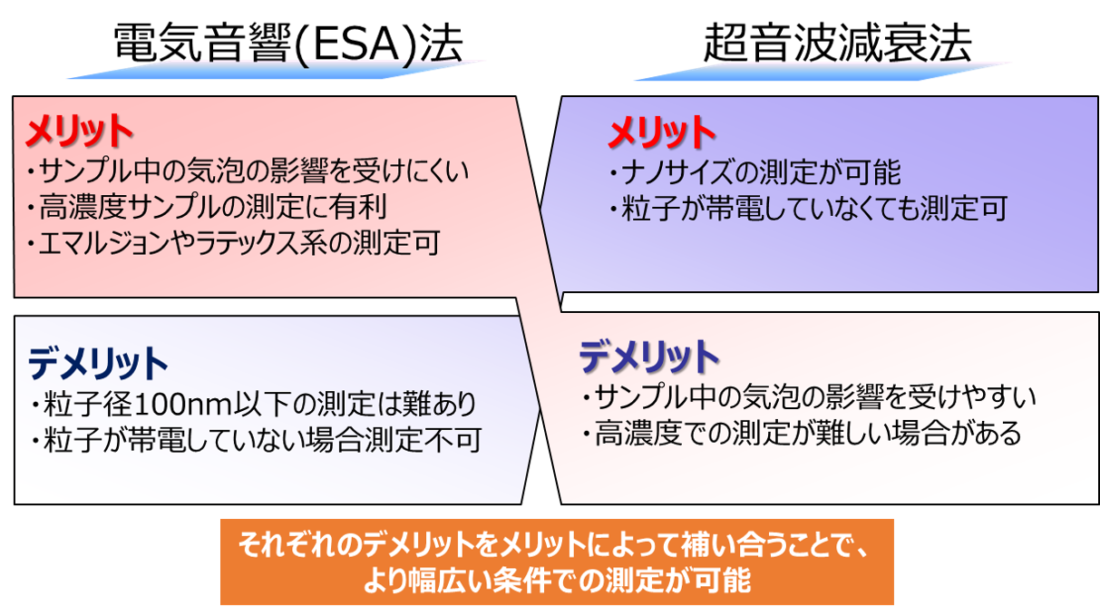
測定精度の再現性
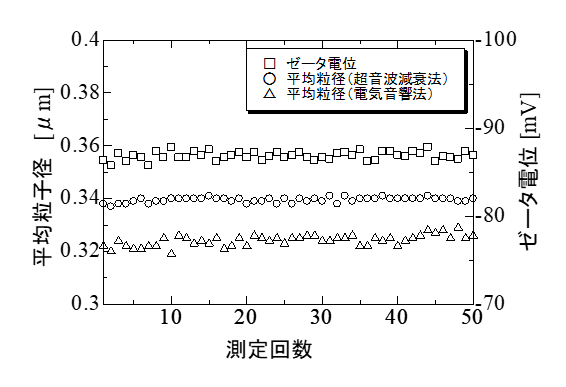
インライン測定器の粒度分布およびゼータ電位測定精度の再現性を確認するために、分散状態が安定した3 wt.%のコロイダルシリカを用いて50回繰り返し測定を行った結果を示します。粒度分布測定では超音波減衰法ならびに電気音響法ともに平均粒子径が±0.01 μm以内に、そして、ゼータ電位も±1 mV以内に収まっていることから、非常に高い再現性で測定できていることが分かります。
ビーズミルとインライン測定器を組み合わせた新しいシステム (特許第 5248801)
ビーズミルとインライン測定器を組み合わせたシステムを紹介します。下記は、当社にて使用したシステムの一例です。サンプルはホールディングタンク下部からインライン測定器に取り込むようにしています。これは、サンプル内に測定誤差の原因になる気泡の巻き込みを防ぐ事と、サンプルの急激な温度変化および高温化を避けるためです。
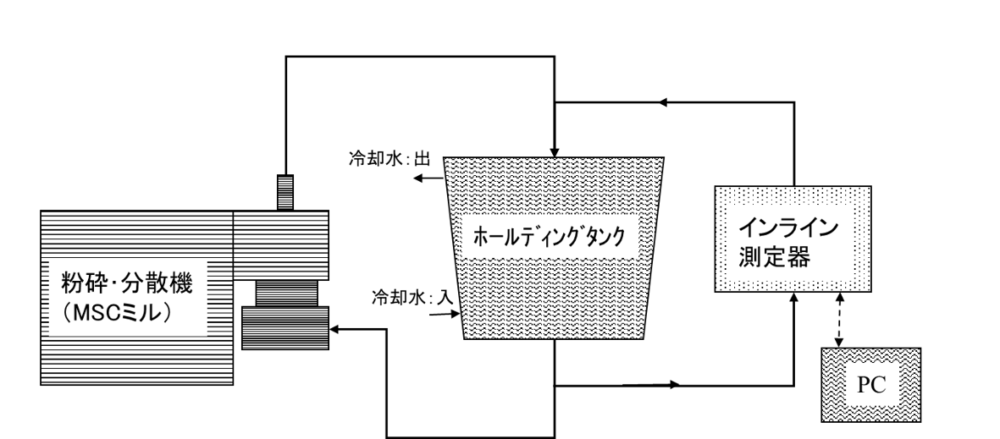
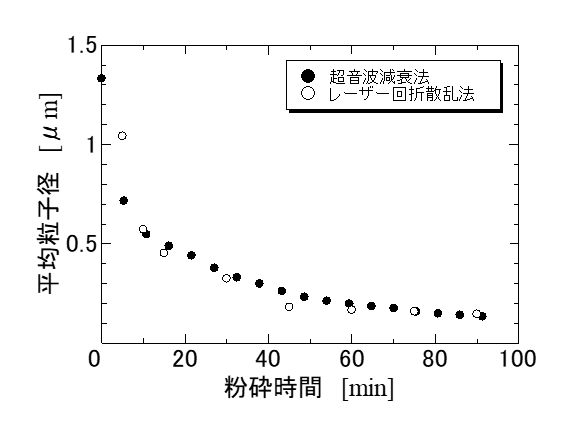
粒子濃度が10 wt.%、分散剤を粉末ベースで4%添加し調整したスラリを原料として、インライン測定を行いながら炭酸カルシウムの粉砕試験を行いました。途中サンプリングを行いながらレーザー回折・散乱式測定でも粒度分布の測定を行い、超音波減衰法での測定結果との相関性を確認しました。平均粒子径、粉砕傾向ともにレーザー回折・散乱法測定と同様の結果が得られていることがわかります。
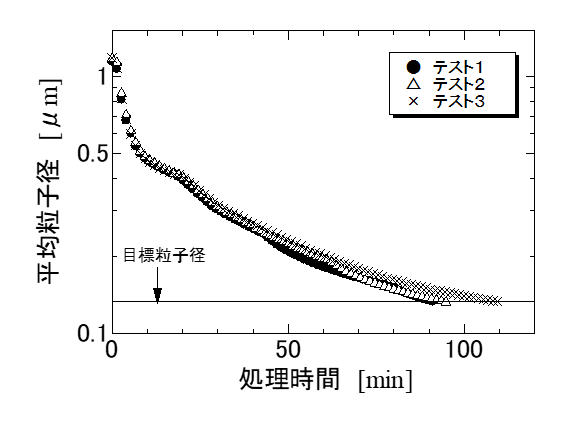
次に、粒子濃度10 wt.%で分散剤を粉末ベースで2~4%添加し調整したスラリを原料に用いて、3回粉砕試験を行った結果を示します。目標粒子径をテスト1の回収時粒子径に設定し(インライン測定で平均粒子径が0.1334 μm、レーザー回折・散乱法測定で0.145 μm)、テスト2,3ではインライン測定結果が目標粒子径以下になった時点で、ビーズミルを停止して製品を回収しました。その際、レーザー回折・散乱法測定でも粒子径の確認を行いました。
下表、テスト2,3で回収した製品はレーザー回折・散乱法測定の結果からも、目標粒子径の0.14 μm台にしっかりと収まっていることが分かり、インライン測定器で仕上がり製品の粒子径を制御できることが確認できました。

参考:椎名啓, 粉体と工業VOL40, No.9, インライン測定システムを用いた粉砕分散処理の制御ならびに解析技術, (2008)
機器導入に関してのご相談から専門的な技術セミナーまで
様々なシチュエーションに対応します。
技術情報には掲載していない情報もお伝えすることができますので、
当社機器にご興味を持たれた方は是非お問い合わせください。