シリコンからの水素製造技術(装置)の紹介
はじめに
カーボンニュートラル実現に向けクリーンなエネルギー源として期待される水素ですが、その製造には化石燃料を原料とする製法や、製造過程で二酸化炭素を排出するプロセスにより製造された水素が価格も安く、安定供給されていることから、現在これらの製法が主流となっています。一方で、最もクリーンな水素として期待されるグリーン水素(再生可能エネルギーで水電解法等により製造された水素)は、製造コストが高いことから普及が遅れています。今回、当社が開発した装置は、廃棄されているシリコン、そして水とアルカリを原料として水素が製造できる新たなプロセスを採用し、また、装置の電源にグリーン電力を用いることでグリーン水素の製造が可能となります。さらに、水電解法と比べて水素製造に掛かる電気消費量も少なく、環境負荷の少ない、そして低コストで水素を製造する方法として期待されます。
製造原理とプロセス
水素製造方法は、アルカリを加えた水の中でシリコンを粉砕し、発生したガスを回収して水素を精製するプロセスとなります。粉砕にはボールミルやビーズミルと呼ばれる粉砕機を用いることで、メカノケミカル反応*¹を利用して化学反応を促進させることで水素発生量を増大させます。また、ここで用いる粉砕機の電力は水素製造に要する製造コストに大きく影響することから、より効率の良い粉砕機の適用と粉砕条件の最適化が求められます。この水素製造プロセスの要となるシリコンの粉砕工程へ、当社が長年培ってきた粉砕技術を投入し、より効率良く、より大量に水素を製造するシステムを完成させました。
シリコンが粉砕されると、微細化によってシリコン粒子の表面積が増大し、水と接する面積が増える(反応場が増える)のと同時に、粉砕時にシリコン粒子に付与された機械的エネルギーによってシリコン粒子表面が活性な状態となり、水とより反応しやすくなります。粉砕され活性化されたシリコン粒子は、水から酸素を奪って酸化し、その結果、水素ガスが発生します。また、水にNaOHやKOH等のアルカリを添加してpHをアルカリにすることでシリコンとの反応がより促進され、反応速度や水素ガスの発生量を増大させることができます。反応には様々な経路が考えられますが、このプロセスの化学反応式を簡単に表現すると以下の様になります。
<反応式> Si + 2ROH + H₂O → R₂O₂Si + 2H₂
水の電気分解では水素ガスの他に酸素ガスも発生しますが、このプロセスでは酸素ガスはシリコンの酸化で消費されるため、ほとんど発生しません。したがって、ガス発生後の水素精製プロセスの簡略化が可能となり、設備コストや運用コストの削減に繋がります。さらに、この反応は常温・常圧下で進行するため、高圧ガス保安法等の規制を受けず、専用の設備設計が不要で運用面での規制も受けませんので、設備導入のハードルが下げるだけでなく、運用コストも抑えることができます。
プロセスの代表的なフローを図1に示します。粉砕によって発生したガスは水素の純度が高いため、その後の精製工程もフィルターを通過させる程度で燃料電池用水素ガスの品質基準であるISO14687 Grade-Dをクリアできる純度まで高めることができます。なお、この水素製造方法、装置については特許技術 (特許第7291756号) が用いられています。
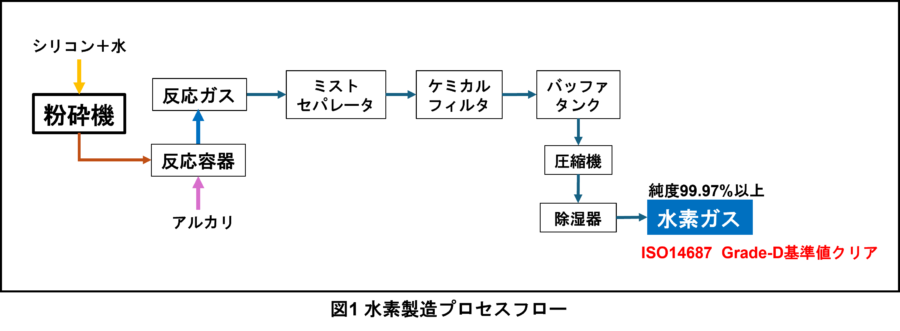
水素生成量
図2に示す装置でシリコンと水、アルカリから水素ガスを発生する実験を行いました。その結果、粒度150ミクロン以下、純度95%以上のシリコン粉末1gあたり約1.6ℓの水素ガスを生成することができました(図3参照)。シリコン廃棄物の粒度や純度は様々ですので、実際はこれよりも生成量は少なくなるものと考えますが、より高純度なシリコン廃棄物使用することで、この実験値に近づけることは可能です。半導体素材の製造過程で排出されたシリコンスラッジ(不純物含む)を用いた水素製造試験では、1トンのシリコン廃棄物から約50kgの水素を生成した実績もあります。

水素製造に要する電力量
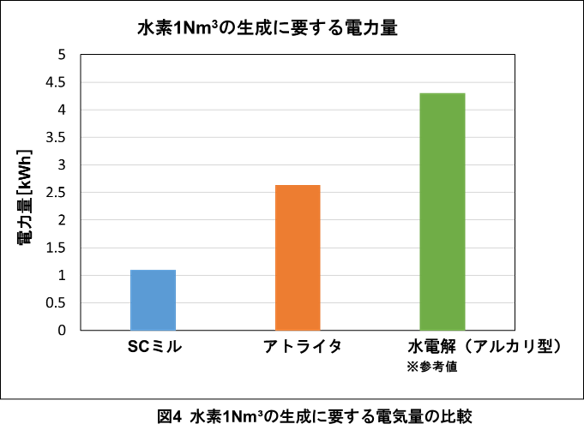
粉砕機に「SCミル」(ビーズミル)と「アトライタ」(ボールミル)の2機種を用いてシリコンを粉砕し、1Nm³の水素を生成するのに要する電力量を比較しました。シリコンは粒度150ミクロン以下、純度95%以上のシリコン粉末を用いました。結果を図4に示します。「アトライタ」では約2.6kWhの電力量を要したのに対し、「SCミル」では約1.1kWhの低電力量で済みました。原料の素性に合わせた粉砕機ならびに処理条件の最適化がエネルギー効率や製造能力に影響を及ぼすことが分かります。一方で、アルカリ型水電解装置で1Nm³の水素を製造するのに要する電力量として、経済産業省が公表している資料*²を参考にしますと、約4.3~5.0kWhとなりますので、当社プロセスではアルカリ型水電解法と比較して約1/4の電力量で水素を製造することができます。ただし、このデータは一例であり、シリコンの粒度や純度によっても単位水素生成量当たりの消費電気量は変わりますので参考値として捉えてください。
*2・・・ 水素・燃料電池戦略ロードマップの達成に向けた対応状況 資料1 (2020年6月8日)
https://www.meti.go.jp/shingikai/energy_environment/suiso_nenryo/roadmap_hyoka_wg/pdf/002_01_00.pdf
原料となるシリコンは?
高純度な金属シリコンは価格も高く、これを原料として水素を製造することは望ましくありません。高純度なシリコンが使われている製品の代表例が、半導体や太陽電池です。例えば、半導体の基材となるシリコンウェハの製造過程では、シリコンインゴットからウェハをスライス加工する工程で多量の切削屑が発生します。太陽光発電用セルの製造過程でも同様にシリコンインゴットからスライス加工する工程で大量の切削屑が発生し、これらの切削屑は粒度が細かく、また不純物も混入しているため、半導体用や太陽光パネル用の原料としてのリサイクルは技術的、コスト的にも厳しく、現状はそれらの多くが産業廃棄物として処分されていますので、この廃棄されている高純度シリコンを原料とすることで、安価に水素を製造できるだけでなく、廃棄物の再利用による環境負荷低減にも繋がります。
また、近年懸案となっている太陽光パネルのリサイクルですが、2030年代後半から太陽光パネルが大量に廃棄され始めることが予測されており、日本国政府も太陽光パネルのリサイクル義務化の検討を進めています。太陽光パネルのリサイクル技術は各種開発が進められており、経済産業省が公表している資料*3によれば、太陽光パネルを構成する部材の中でも8割以上の重量比を占めるアルミフレームとガラスに至っては、様々なリサイクル技術が開発され、実際にリサイクルが行われておりますが、セル/EVAシートのリサイクルに関しては技術的な課題が多く、また、費用面からも現状は精錬等によってセル/EVAシートに含有する銀や銅などの高付加価値金属の回収に留まり、シリコンや樹脂類は精錬の際の熱源としての利用に留まっています。
そこで、当社ではセル/EVAシートから安価にシリコンと樹脂を分別回収するプロセスを独自に開発し、特許を出願しております(特開2025-023654)。このプロセスを用いることで、セル/EVAシートに含まれるシリコンを最大約87%回収することができました(図5参照)。また、太陽光パネルから回収したシリコンを原料にして、ここで紹介した水素製造プロセスによって実際に水素ガスを発生させることにも成功しております。試験を進める中でいくつかの課題も見つかりましたが、プロセスの一部を改善することで十分に解決できるものと考えます。
今後の太陽光パネル大量廃棄時代およびリサイクル義務化の流れを鑑み、ここで紹介した太陽光パネルからのシリコン回収技術と、シリコンからの水素製造技術を掛け合わせることによる相乗効果は大きいと考えられ、カーボンニュートラルならびに資源循環型社会へ当社が技術的に貢献できることを期待しています。
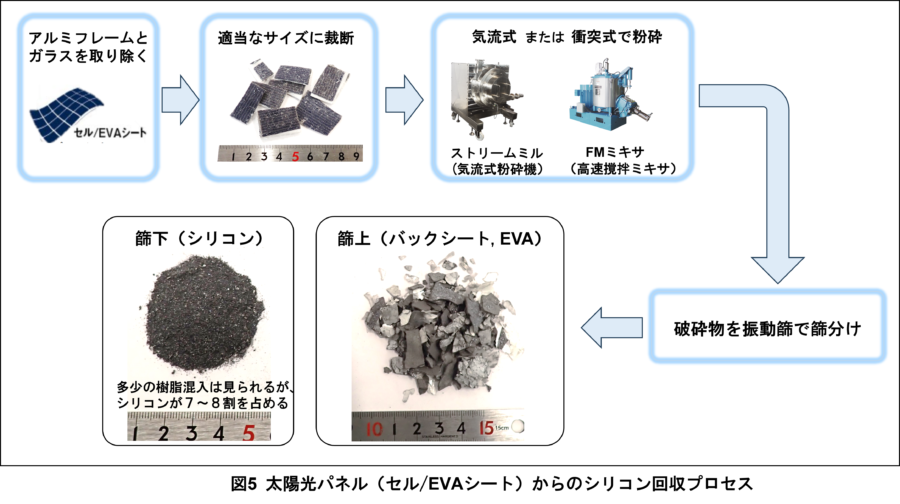
*3・・・ 太陽光発電設備の廃棄・リサイクルをめぐる状況及び論点について 資料3 https://www.meti.go.jp/shingikai/sankoshin/sangyo_gijutsu/resource_circulation/solar_power_generation/pdf/001_03_00.pdf
水素製造設備(装置)の特徴
当社が開発した水素製造プロセスは、シリコンと水、アルカリ、そして電気があれば特に場所を選ばずに水素を製造することができます。また、水素生成から精製までの全プロセスを1MPa未満の低圧下で運用できるので高圧ガス保安法も適用されず、設備導入や運用面でのハードルは非常に下がります。さらに、設備の電装品を防爆仕様にすることで屋内での水素製造も可能となります(貯蔵は屋外)。
水素のコストが増加する要因の一つに、高圧での貯蔵ならびに運搬が挙げられます。低圧下で製造した水素を高圧まで圧縮せずに、製造所付近に一定量の低圧貯蔵タンクを設け、そのまま水素を消費することができれば圧縮・充填設備も不要で、さらに高圧ガスを取扱う為の保安距離確保や建造物の構造、保安要員などの人件費も不要となり、イニシャル・運用コストを削減できます。
当社の水素製造装置はお客様が求める製造(消費)規模に合わせて、小規模から大型設備まで対応いたします。例えば、水素生成量の項で説明した粉末シリコン(粒度:150μm以下、純度:95%以上)を用いて水素製造する場合、水素製造能力が0.2~0.5Nm³/hの小型装置から、40~100Nm³/hの大型設備までが標準的なスケール範囲となりますが、それ以上の製造規模を望まれる場合はラインを複数併設することで対応できます。今後は設備のユニット化やパッケージング化などの検討も進め、より導入しやすい製品へ発展させていきたいと考えています。また、この水素製造設備はシリコンの排出源と水素の消費先が隣接している場所への導入が理想的ではありますが(地産地消型)、水素の貯蔵・運搬と比べるとシリコンの運搬の方がコストや安全面でも有利であることから、例えば、水素需要先に当設備を設置し、原料となるシリコン廃材を搬入・保管しておき、必要な時に水素を製造・消費する形態にも適しています。また、水素を製造した後のシリコン化合物の残渣に関しましても、セメント原料や路盤材へのリサイクルの検討も進めており、当設備によってシリコン廃棄物からグリーンな水素を製造し消費することで、カーボンニュートラルや資源循環型社会への貢献が図られるものと期待しています。
機器導入に関してのご相談から専門的な技術セミナーまで
様々なシチュエーションに対応します。
技術情報には掲載していない情報もお伝えすることができますので、
当社機器にご興味を持たれた方は是非お問い合わせください。